Continuing from Vol.1, in the previous issue, Hama-san happened to see me on NHK Nagano and thought to himself, "Maybe if I met this person, I could dye deerskin?", and then I contacted Hama-san myself, which was how we met miraculously.
I wanted to increase the added value of this deerskin by dyeing it with indigo, so out of the many indigo dyeing workshops out there, I was drawn to the historic Hamasome Workshop and made an appointment.
Before I go any further, let me tell you a little about Hamasome Kobo.
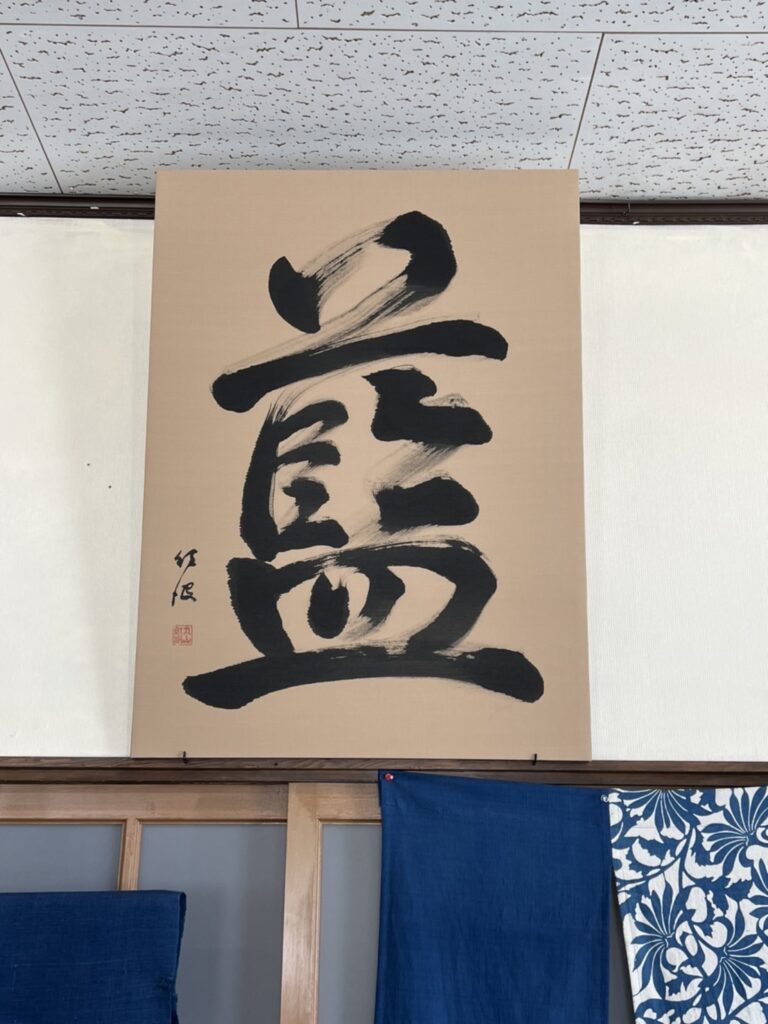
Hama Dyeing Studio is a dyeing studio located in Aihajicho, Matsumoto City, founded in 1911.
Located very close to Matsumoto Castle, the town was home to over 100 indigo dye artisans when it was founded . Now, there is only one left!
This is a historic workshop that must be protected.
The first "Plant Dyeing and Weaving Exhibition" was held at the Ginza Shiseido Gallery in 1932, and its initiator was Shimazaki Toson. The list of exhibitors included leading cultural figures of the time such as Arishima Ikuma, Tomimoto Kenkichi, Takeshita Yumeji, Mizutanigawa Chuma, and Nakamura Shuuka. The history of the exhibition is so long that the name of the founder of Hama Dyeing Studio, Hama Shigeto, was also included in the list.
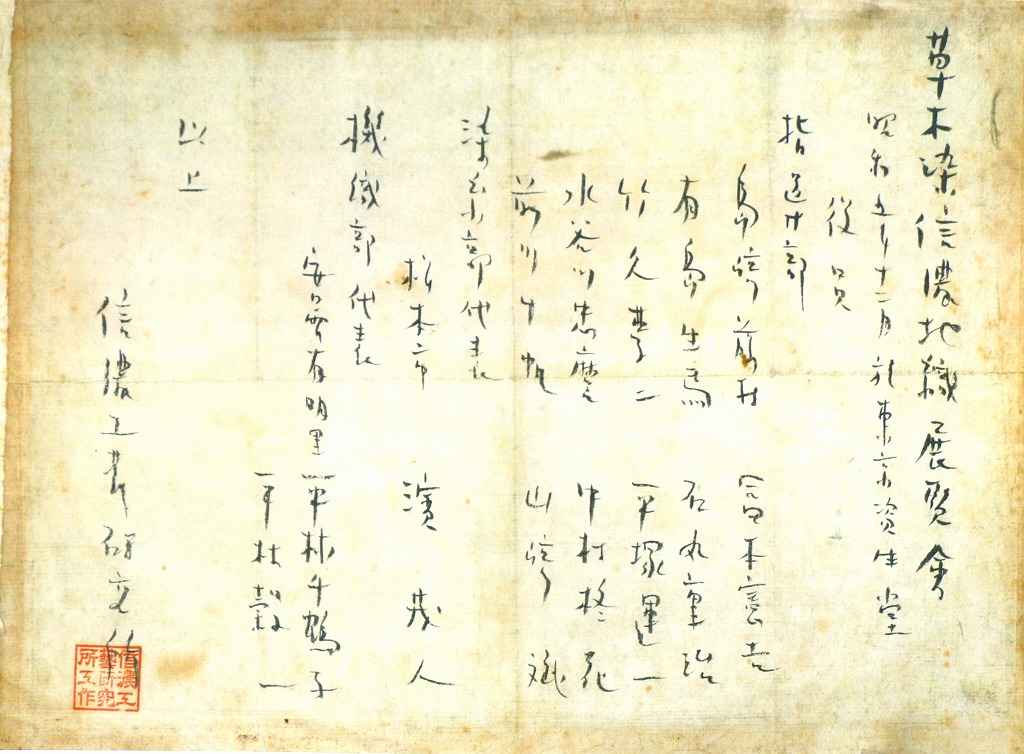
Just looking at this, it is clear that the first generation was quite famous in the world of plant dyeing, but when you listen to his story, there are many things that he did that are not recorded in books, and you get the impression that he was a man of true craftsmanship.
When I decided to have Hama-san dye the game leather with indigo, I knew about the information from 1911, but I never imagined he would be such an influential person in the plant dyeing world...I am truly honored!
Produced in collaboration with Mersen Co., Ltd.
I went to meet Hama in July 2022 and realized that we needed the help of a leather expert to really move forward.
I had spoken to Mersen's Managing Director Nakagawa about Hama-san in advance, and we had been constantly discussing and consulting each other about the progress of the situation.
First of all, we couldn't do anything without the materials, so we asked Managing Director Nakagawa to send us the chrome-tanned and vegetable tanned fabrics, and we took them to Hama-san the following month in September.
On that day, I wanted to try out indigo dyeing a little bit, so I took a T-shirt indigo dyeing experience class! But I'll write about that in another article.
Hama-san had the dyeing done between work, so time passed and in December we received a message that the dyeing was finally complete. On that day, we also had Mr. Nakagawa, the senior managing director of Mersen Co., Ltd., come.
It was here that I got to see Hama-san's pot dyeing of bolts of cloth for the first time!
This vase was made by the previous owner and Hama-san made it even higher and deeper.
You can't tell how deep it is in the photo, but when Hama-san falls in he completely sinks lol
Apparently it is buried nearly 1.8 metres underground!
This is the heart of the indigo dyeing process!!
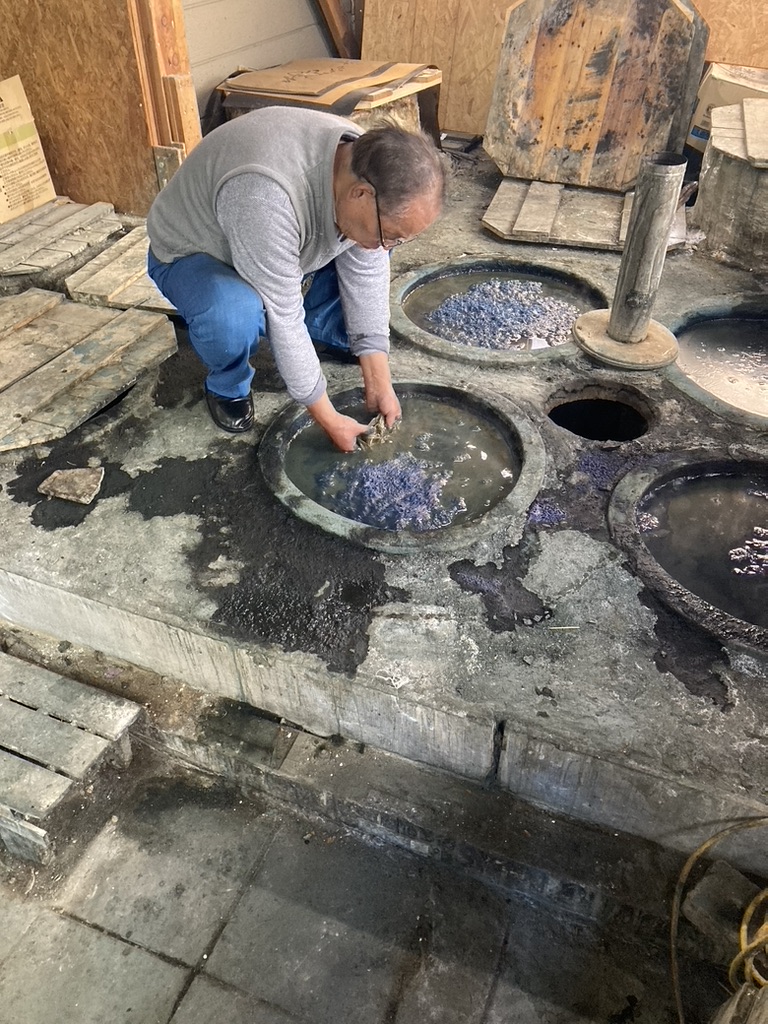
In the photo, there is a small hole in the middle of the four jars, and through this you can see the red-hot ashes used to heat the jars.
In order to keep the indigo dye at a constant temperature, when it gets cold, the temperature of this pot must be checked twice a day! Because of this, he was unable to go anywhere in the winter, and was even unable to attend his son's wedding.
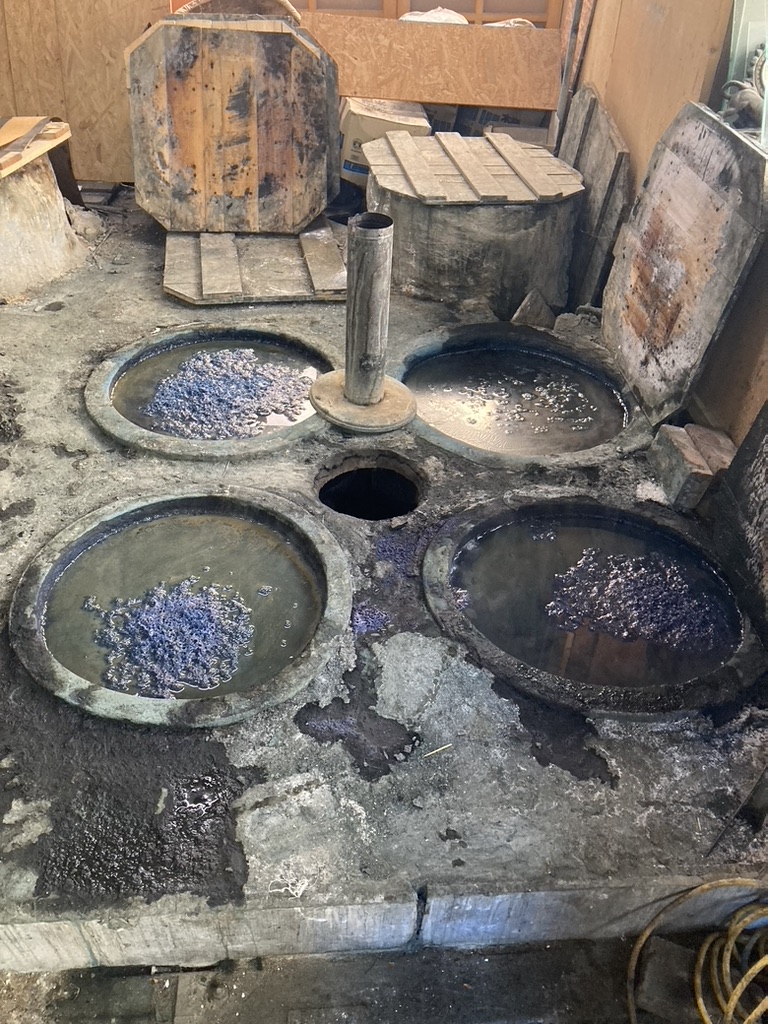
In the summer, too, there are many problems as the food will rot if it gets too hot, and in recent years global warming has caused various problems.
However, every time I come here I feel like I am touching history, a Showa era feeling that I have forgotten, or perhaps a feeling even older than that.

What we were able to see on this day was plain indigo dye (the navy blue leather below), and you can see that it was dyed beautifully!
And that camel and navy checkered thing on top?
This is actually "stencil dyeing with indigo dye" !!
I received a message that the dye had been applied and I was going to check it out, but it turned out to be stencil dyeing!?
Hama-san's wife decided to give it a try and tried stencil dyeing using some scraps of Shinshu deerskin (camel leather) that I had given her, and to her surprise, the dye came out!
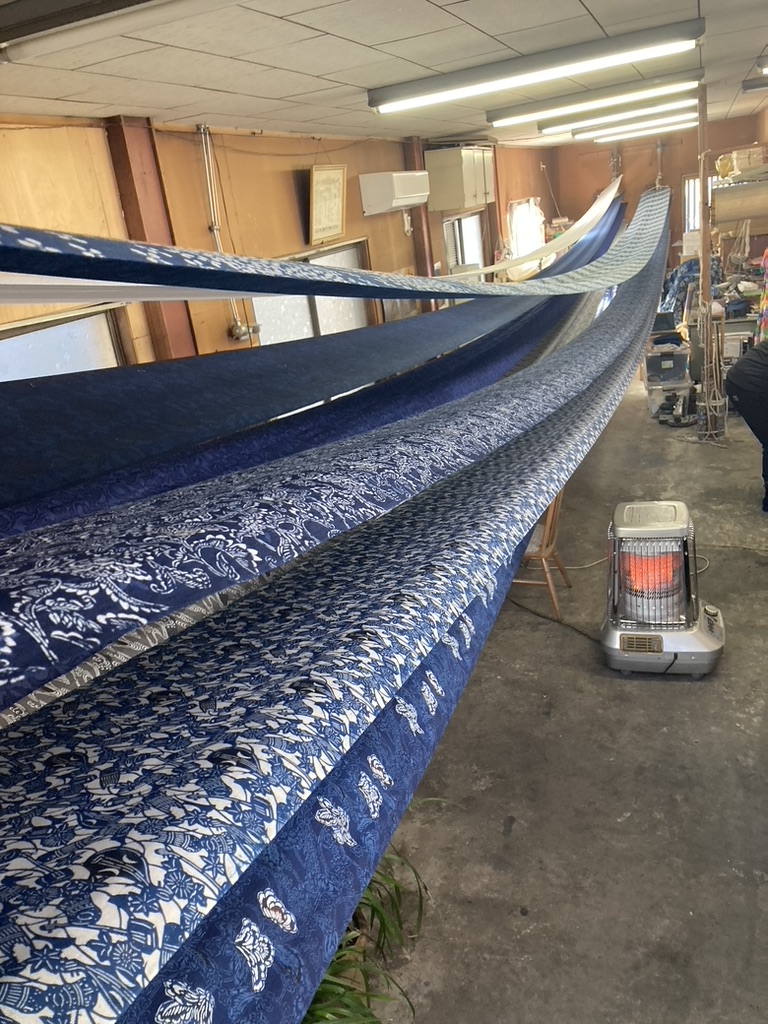
This is stencil dyeing of cloth!
I was surprised when I first saw this!
It's quite surprising when something that you thought was impossible is right in front of you.
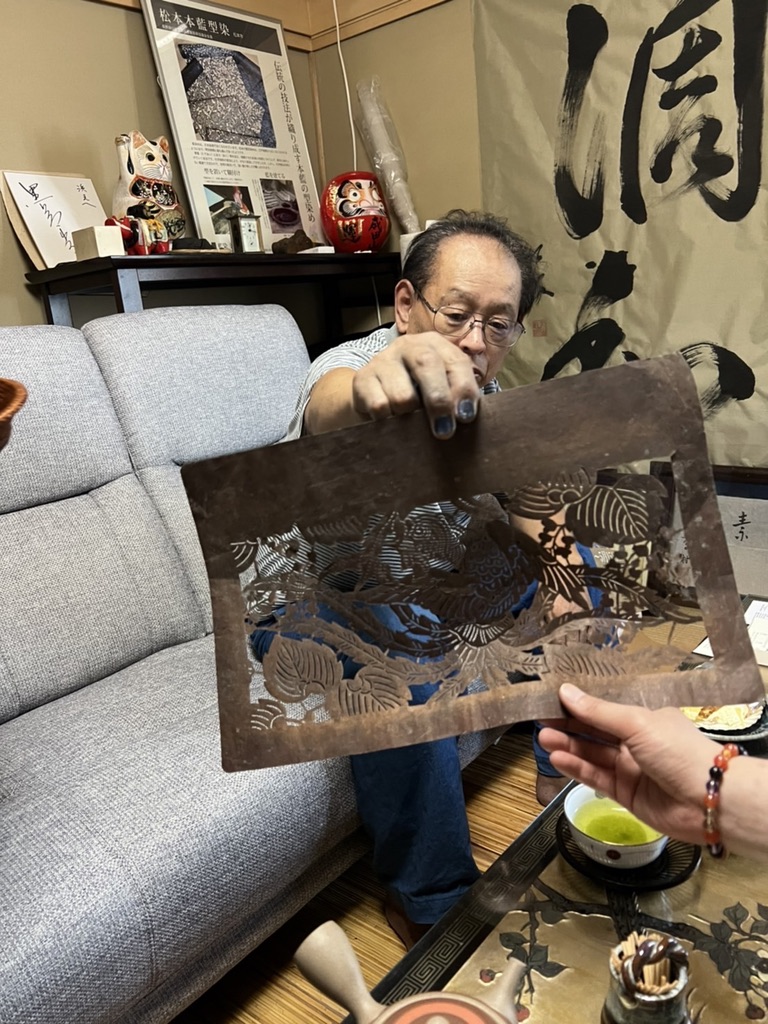
This seems to be something made by applying persimmon tannins to stencil-dyed Japanese paper, and this photo appears to be quite old.
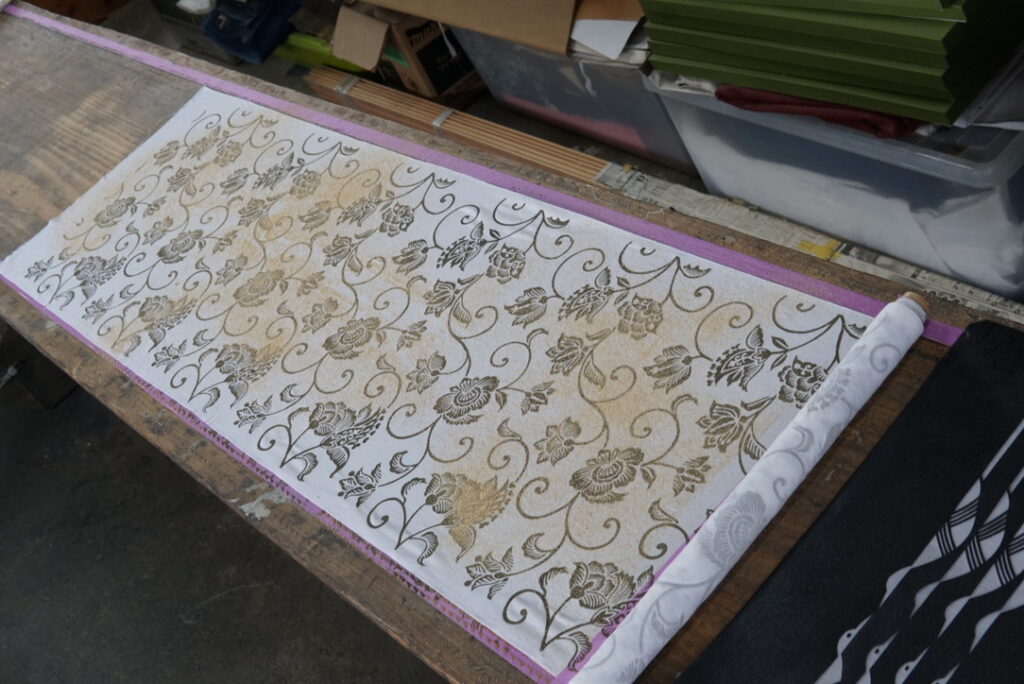
The above photo shows white fabric with the dye-resistant paste applied. The molds are layered repeatedly, which requires considerable skill, but actually making the dye-resistant paste is more important, as it takes five years of training just to make the paste and three years to apply it.
The starched fabric is then dipped into the pot several times, and when the glue is washed off, those areas are not dyed blue, revealing the pattern.
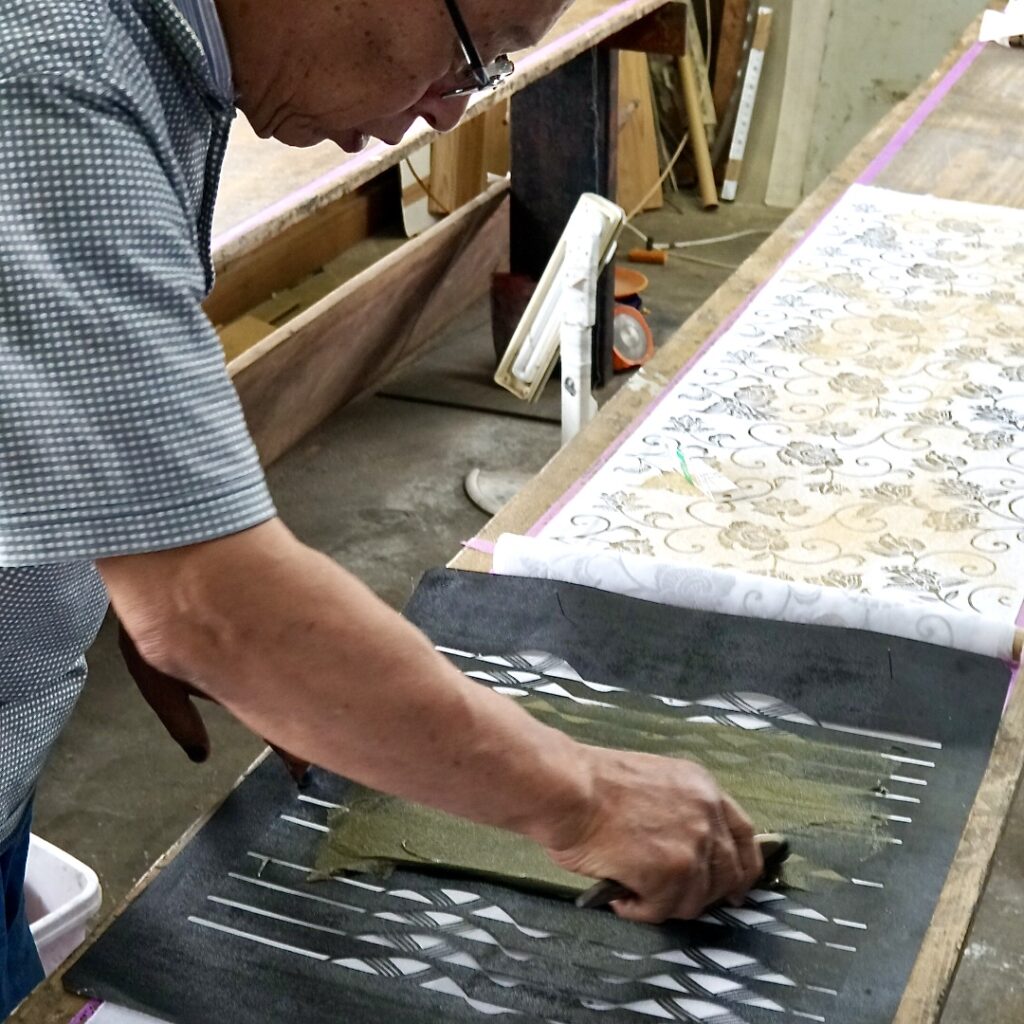
this!
I actually borrowed it and tried it out.
It can get pretty uneven (・_・; Of course it's not that easy.
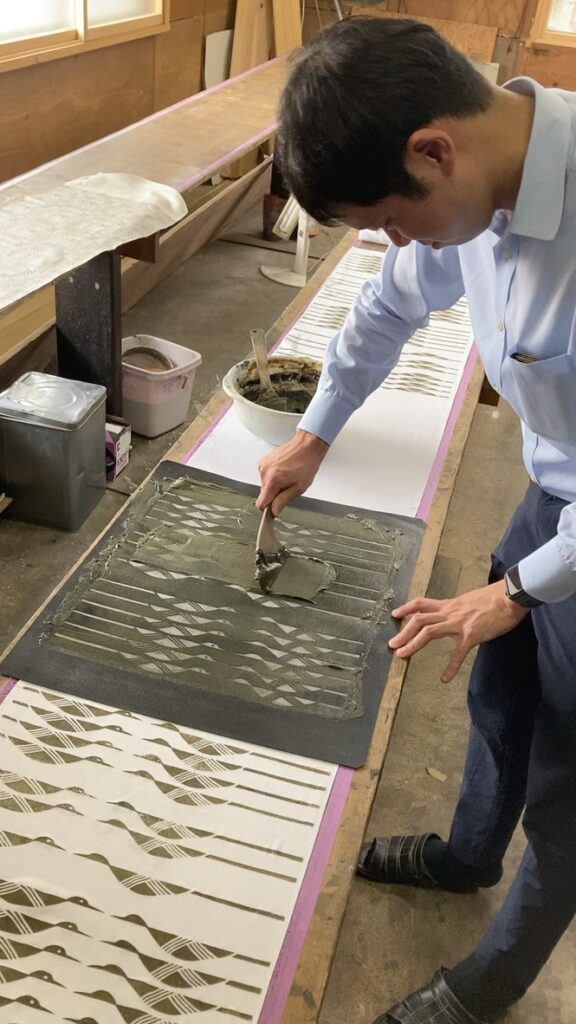
This is Mr. Matsushita from NHK Nagano Broadcasting Station. I know it's rude to use Mr. Matsushita as an example, but you can see that it's very gaudy, right?
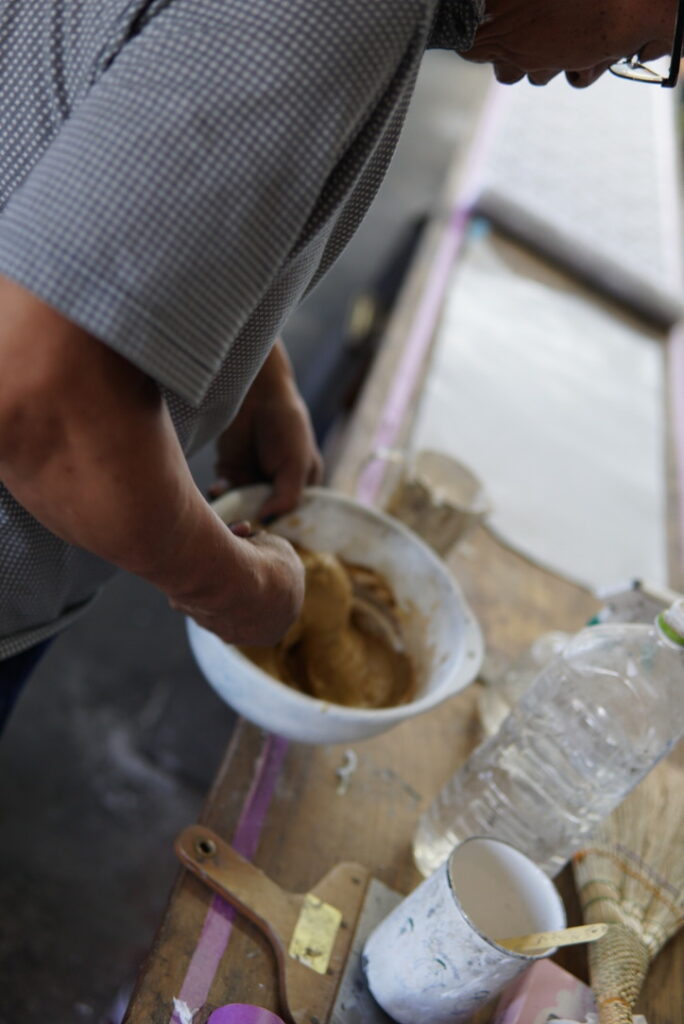
The photo shows the process of kneading the dye-resistant glue, which has taken five years to make!
In fact, Hama-san makes about three but can only use one of them!
It seems like he's not happy with the rest and throws them away!!
What's more, the formula for this glue has been altered slightly to ensure it adheres well to the leather, making it even more difficult!
I'm really grateful for your cooperation (;;)
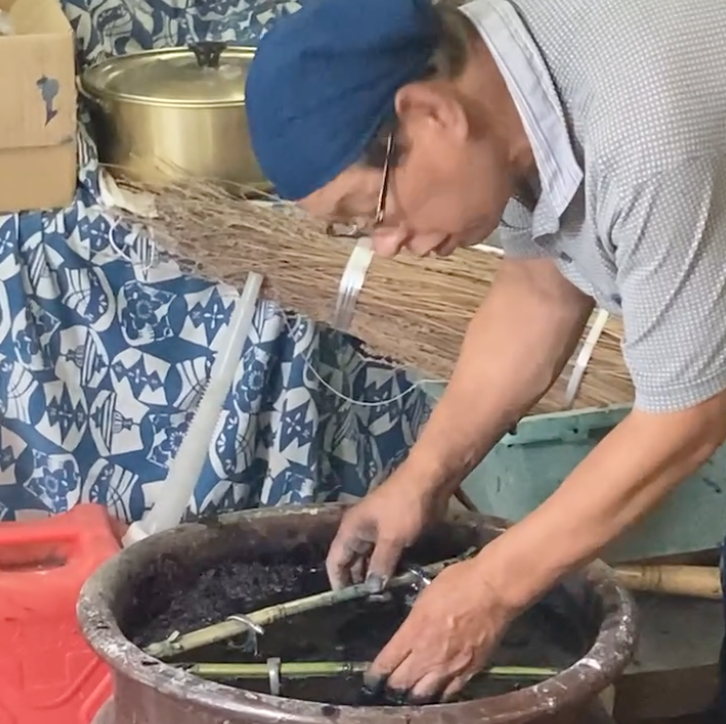
I'll put this in the pot
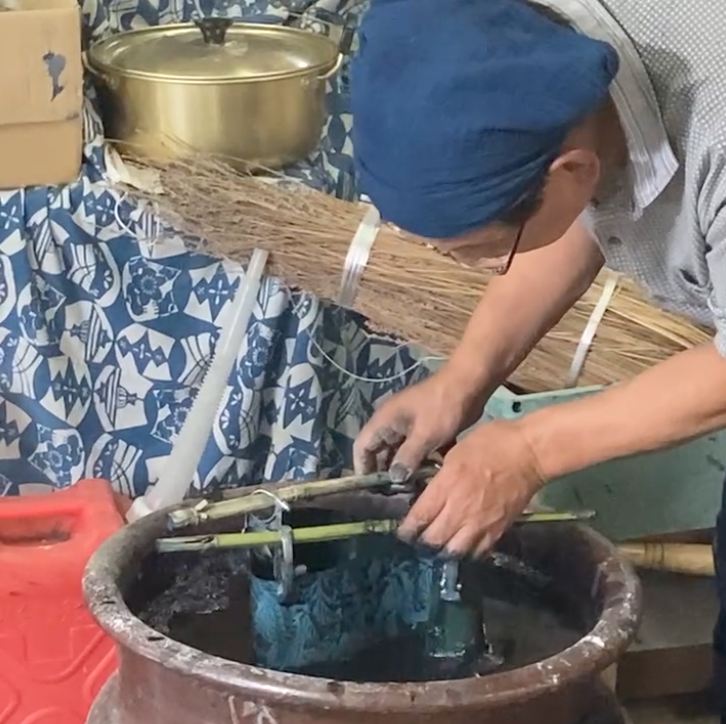
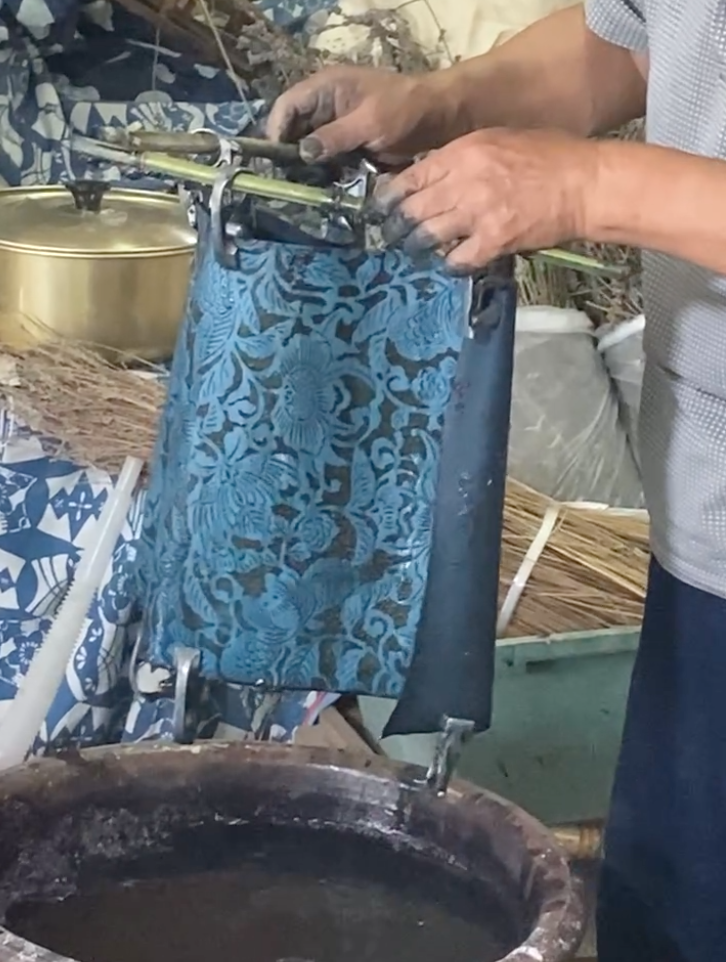
When you take it out of the jar and it comes into contact with oxygen, it turns blue.
I do this three times, but if I do it more than that the glue will come off.
Another problem is that in winter the glue cracks and it doesn't work well, and in summer it's too hot and the glue drips and it doesn't work ^^;
Therefore, we had to wait until the hot days of midsummer to take this photo, and because this year's summer was particularly long, it was difficult to dye the leather. Considering that, this leather is quite rare!!
Even in this day and age when you can get anything you want, I've created something rare and hard to find!
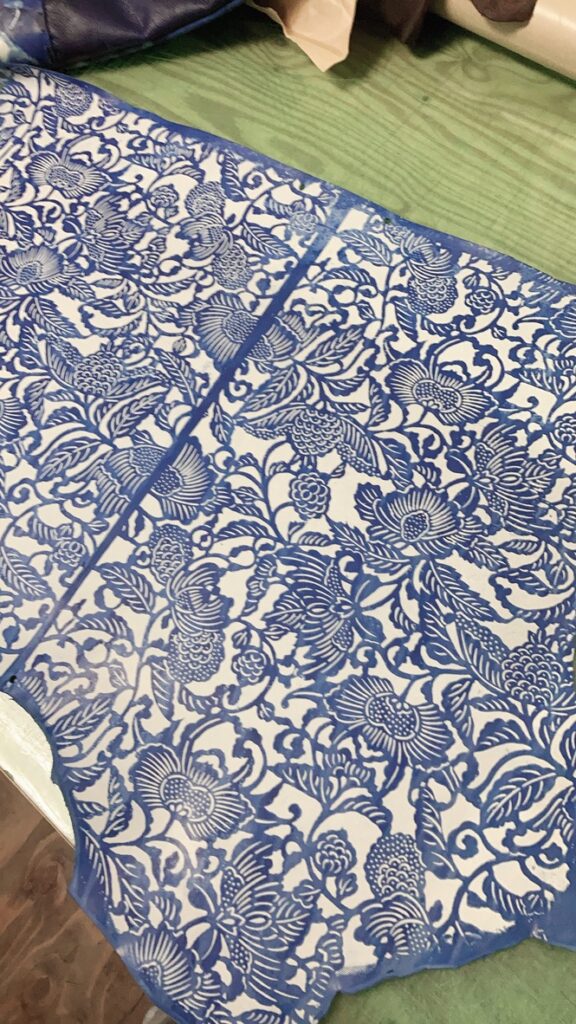
It's always nerve-wracking to put a knife to this leather, which contains the thoughts of these three companies!
And my desire to share this feeling with people all over the country and the world is growing!
Live commerce in Singapore
In fact, the first sale of this leather product was in Singapore!
A famous person like Nakai-kun in Japan came to Japan and sold something on live commerce.
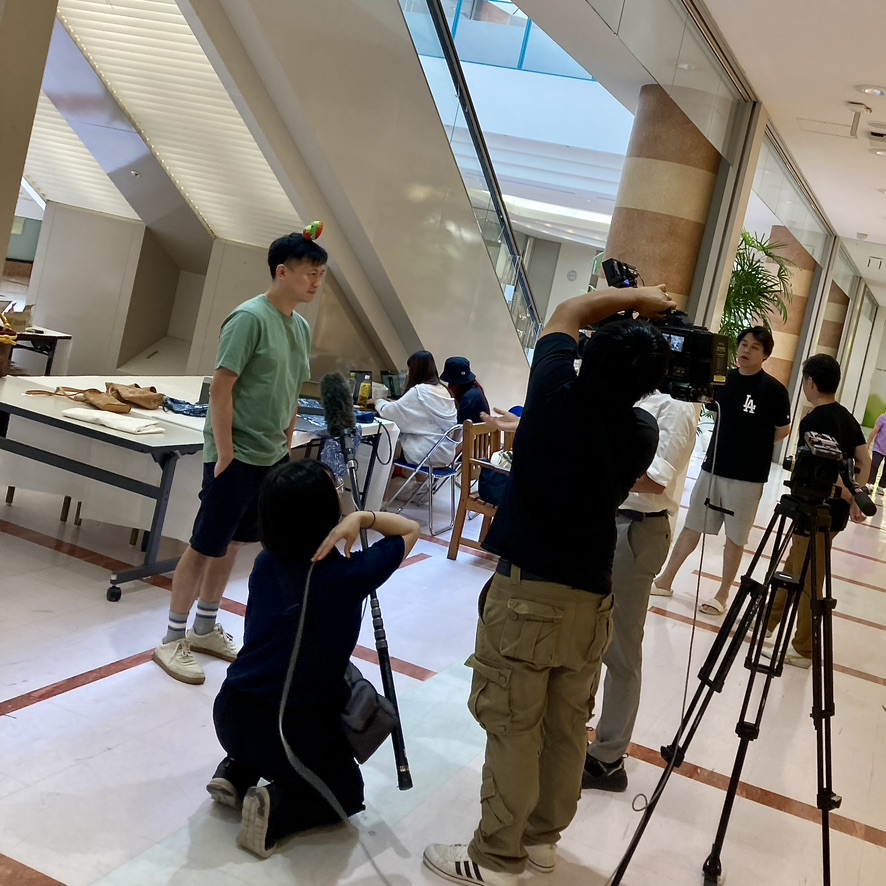
The venue is Icity 21 in Yamagata Village, Matsumoto City.
The Pongsak Camera that the green guy is working with in Singapore is also run by Mr. Matsushita for the NHK Nagano Broadcasting Station!!
When we mentioned that there would be live commerce during our in-depth coverage, they said they would definitely like to cover it, so we made it onto the air!
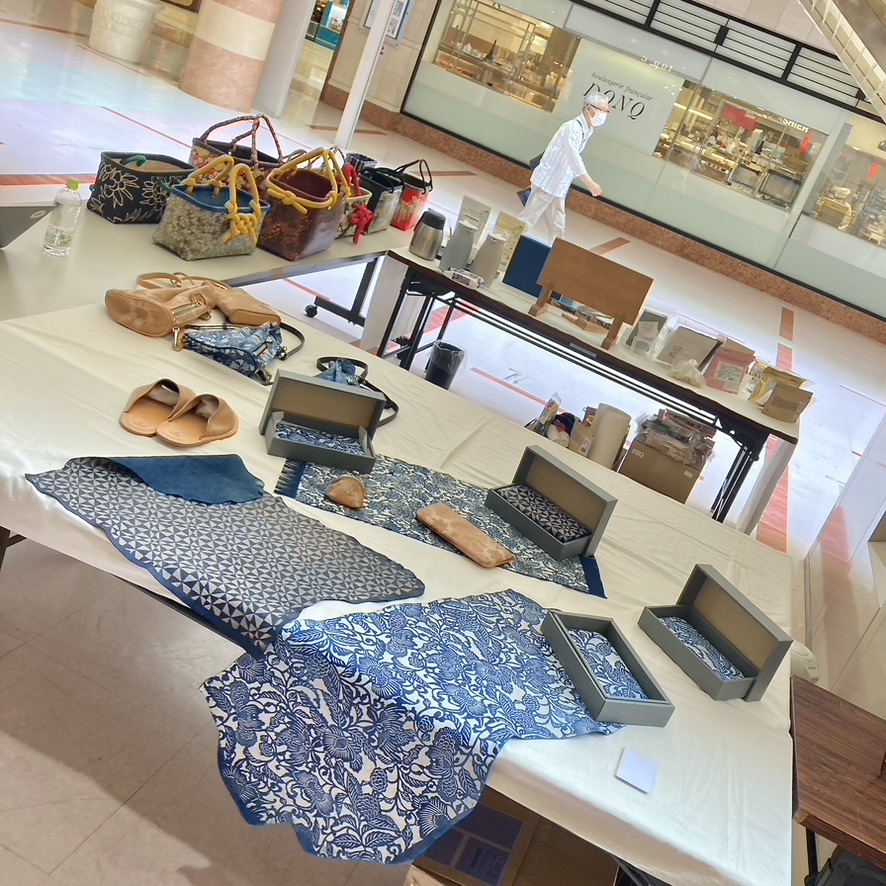
My long-awaited overseas sales were in Singapore (^○^)
Nowadays, we live in an internet society where there are many ways to sell things, and in order to preserve the techniques of traditional craftsmen, it is important to connect them to sales! I mean this without flattery!
We live in an age where you can get anything you want online, but if you're going to buy something, I want you to try and get something that has meaning and a story behind it!
Our challenge continues!
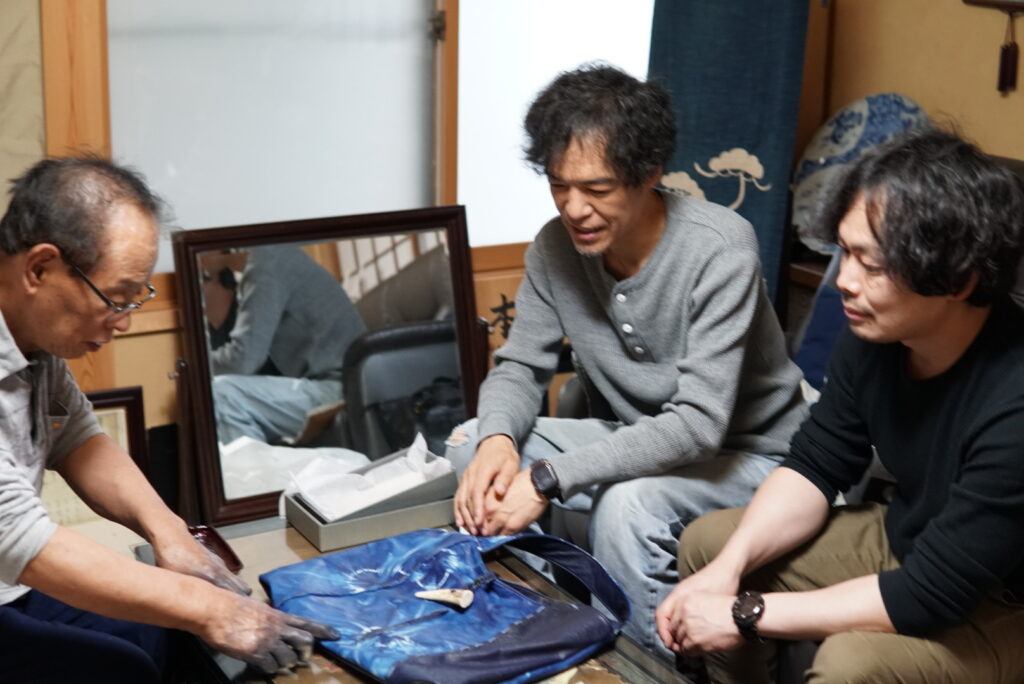
On the left is Mr. Kanji Hama from Hama Dyeing Studio, on the bottom right is Managing Director Nakagawa from Mersen Co., Ltd. (Tanner), and on the top right is Tokunaga from Gruber Leather.
This is a photo of us checking out the finished bag after the challenge began, but we have been working on this project for over a year.
Whenever Managing Director Nakagawa and I head to Hama's workshop, we cross Aihajime Bridge.
When we had to decide on a name for this leather, Managing Director Nakagawa said, "The character for Aihajibashi would be good, right? How about using this character?" and so we came up with "Aihaji Leather."
The three of them came together to create Aihaji Leather, a name that is fitting for the brand.
I plan to continue trying my best to make this leather into a product that everyone will know in the future!
NHK Nagano has written an article about it.
Please click here to check it out!
NBS has left videos of the apricot-dyed "Apricot Dyed Leather" and "Meihajime Leather" on YouTube, so please click here to check them out!
Click here for Aihaji Leather, Anzu-zome Leather, and Shinshu Deer Leather products.